在运输前进行装运前检验 (PSI) 以进行质量控制
确保在生产运行完成并将您的产品包装准备发货之前,您的产品符合您的要求。
启迈 (QIMA) 的装运前检验是在您生产订单完成 80% 时进行的一项密集现场检查。我们的服务帮助您检查产品是否符合所有要求的规格,使您能够在订单最终确定之前进行纠正措施。
阅读更多关于:
什么是装运前检验 (PSI)?
为什么需要装运前检验?
需要进行哪些检查?
启迈 (QIMA) 的装运前检验 (PSI)
PSI 完成后会发生什么?
启迈QIMA专业技术能力
启迈QIMA优势
什么是装运前检验 (PSI)?
装运前的检查确保您的产品在发货前符合您的质量规格。当至少 80% 的订单完成时,检查员会访问工厂,使用行业标准流程全面审查和测试您的产品。我们的在线平台为您提供完整的报告。
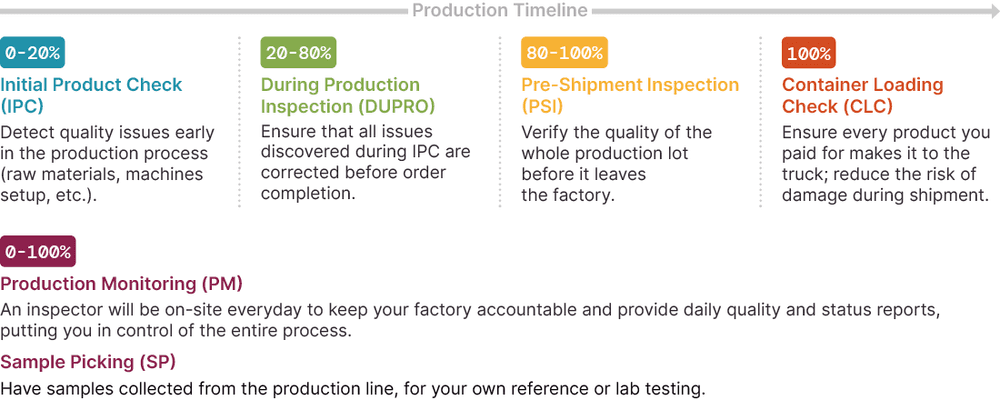
为什么需要装运前检验?
由中立第三方进行的装运前检验是确保产品符合质量规格的行业标准。缺陷或不合格产品可能导致客户投诉、退货、销售损失以及损害公司声誉。
通过我们的装运前检验,您可以放心地知道您的订单在发货前已正确履行。
使用我们装运前检验的几个理由:
确保您的供应商已满足所有商定的规格:这有助于防止误解,确保交付的产品完全符合要求。
使用现成或定制检查清单核实质量标准:根据您的独特标准,可以定制检查清单以满足您的特定需求。
检查生产进度:在延迟影响您的交货计划之前识别任何延误。
在为时已晚之前采取纠正措施:迅速实施解决方案,尽量减少对生产和运输的干扰。
防止退货并保护您的品牌形象:通过确保在发货前的质量,您可降低客户投诉和退货的可能性。
当您无法亲自访问工厂时验证最终产品质量:通过我们的装运前检验,您无需实地在场即可保持质量保证。
依靠您的工厂来告知产品是否符合所有规格并不是一个好主意。我们的PSI专家将提供您生产订单的无偏见、全面的评估。
需要进行哪些检查?
首先,启迈 (QIMA) 检验员将按照 ANSI/ASQ Z1.4-2008 抽样标准随机抽取产品样本进行检验。
在样品被选定后,检查将根据客户需求和特定产品进行定制。
我们提供多种预先设计的适用于不同产品的检查清单,您可以“按原样”使用。您也可以选择通过添加特定检查键修改这些清单,或开发完全满足您特定要求的新清单。
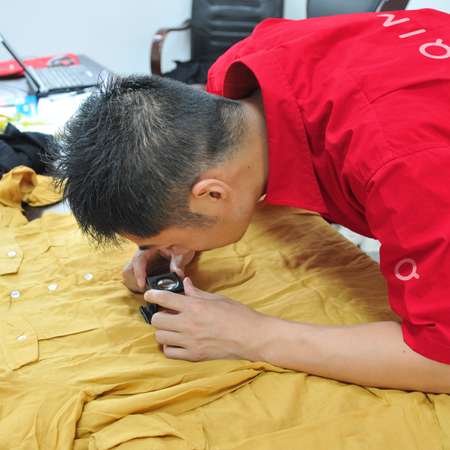
启迈QIMA的装运前检验 (PSI)
启迈QIMA进行全面的装运前检验(PSI),包括一系列细致的检查,通常包括以下内容:
产品规格检查:
半成品、成品和包装产品的数量
产品颜色、风格、结构
艺术品,包括拼写、字体、尺寸、定位和设计
主标签、保养标签、尺寸标签、产品标签
其他产品专用的检查和测试
功能测试
材料成分分析
其他相关测试
工艺缺陷检查
瑕疵检查
组装过程检查
所有产品的一致性
产品尺寸检查
长度、宽度、高度
单重检查
包装和包裹检查:
内外单元包装
出口纸箱尺寸和重量
纸箱上的运输标记
装运前检验完成后会有哪些后续措施?
装运前检验完成后,您将在当日收到一份详细的检验报告。您可以通过启迈QIMA在线账户轻松访问报告。报告详细说明了检验发现,包括任何缺陷的照片,并给出整体的合格/不合格评估。
启迈QIMA专业技术能力
启迈QIMA提供独立的质量控制以保护您的商业利益。我们拥有训练有素且经验丰富的检查员,他们都是产品专家,并在其专业领域定期接受培训。我们的检查员可以在预约后的48小时内到达您的工厂,并在检验当天提供报告。
我们的检验涵盖全系列消费品,包括但不限于服装和鞋类、玩具、电子产品和家具。
在线质量管理
启迈QIMA提供智能在线平台,帮助您无缝管理质量控制和全球供应网络。
只需点击几下,即可轻松预订、取消或重新安排检验项目、付款或下载验货报告。我们还提供一个可定制的数据平台,其中包含您的所有质量控制数据,因此您可以实时识别趋势并做出明智的决策。
启迈QIMA优势
由产品专家进行独立的质量控制,保护您的商业利益。
覆盖全球 100 个国家,包括亚洲、非洲、欧洲、北美和南美。
快速灵活,检验员可在 48 小时内到达现场;最多可在检验前一天修改或取消检验订单。
为您的产品量身定制当日检验报告。
在线计划管理预订检查、付款并下载详细报告。
定制质量仪表板识别趋势并实时做出明智决策。
在行业中排名第一,基于独立的NPS测量,客户满意度最高。